SIMULATION|Finite Element Analysis
Tightly integrated with SOLIDWORKS CAD, SOLIDWORKS Simulation solutions and capabilities
can be a regular part of your design process—reducing the need for
costly prototypes, eliminating rework and delays, and saving time and
development costs.
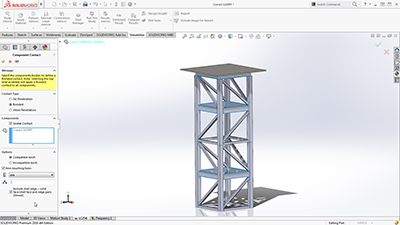
Efficiently optimize and validate each design step using fast-solving, CAD integrated SOLIDWORKS Simulation to ensure quality, performance, and safety.
Finite Element Modeling
SOLIDWORKS Simulation uses the displacement formulation of the finite
element method to calculate component displacements, strains, and
stresses under internal and external loads. The geometry under analysis
is discretized using tetrahedral (3D), triangular (2D), and beam
elements, and solved by either a direct sparse or iterative solver.
SOLIDWORKS Simulation also offers the 2D simplification assumption for
plane stress, plane
strain, extruded, or axisymmetric options. SOLIDWORKS Simulation can use either an h or p adaptive element type, providing a great advantage to designers and engineers as the adaptive method ensures that the solution has converged.
strain, extruded, or axisymmetric options. SOLIDWORKS Simulation can use either an h or p adaptive element type, providing a great advantage to designers and engineers as the adaptive method ensures that the solution has converged.
In order to streamline the model definition, SOLIDWORKS Simulation
automatically generates a shell mesh (2D) for the following geometries:
- Sheet metal body—SOLIDWORKS Simulation assigns the thickness of the shell based on the 3D CAD sheet metal thickness, so Product Designers can leverage the 3D CAD data for Simulation purposes.
- Surface body
For shell meshing, SOLIDWORKS Simulation
offers a productive tool, called the Shell Manager, to manage multiple
shell definitions of your part or assembly document. It improves the
workflow for organizing shells according to type, thickness, or
material, and allows for a better visualization and verification of
shell properties.
SOLIDWORKS Simulation also offers the 2D simplification assumption
for plane stress, plane strain, extruded, or axisymmetric options.
Product Engineers can simplify structural beams to optimize
performance in Simulation to be modeled with beam elements. Straight,
Curved, and tapered Beams are supported. SOLIDWORKS Simulation
automatically converts structural members that are created as weldment
features in 3D CAD as beam elements for quick setup of the simulation
model.
Users can specify local mesh control at vertices, edges, faces, components, and beams for a more accurate representation of the geometry.
Integrated with SOLIDWORKS 3D CAD, finite element analysis using SOLIDWORKS Simulation knows the exact geometry during the meshing process. And the more accurately the mesh matches the product geometry, the more accurate the analysis results will be.
Finite Element Analysis (FEA)
Since the majority of industrial components are made of metal, most
FEA calculations involve metallic components. The analysis of metal
components can be carried out by either linear or nonlinear stress
analysis. Which analysis approach you use depends upon how far you want
to push the design:
- If you want to ensure the geometry remains in the linear elastic range (that is, once the load is removed, the component returns to its original shape), then linear stress analysis may be applied, as long as the rotations and displacements are small relative to the geometry. For such an analysis, factor of safety (FoS) is a common design goal.
- Evaluating the effects of post-yield load cycling on the geometry, a nonlinear stress analysis should be carried out. In this case, the impact of strain hardening on the residual stresses and permanent set (deformation) is of most interest.
The analysis of nonmetallic components (such as, plastic or rubber parts) should be carried out using nonlinear stress analysis
methods, due to their complex load deformation relationship. SOLIDWORKS
Simulation uses FEA methods to calculate the displacements and stresses
in your product due to operational loads such as:
- Forces
- Pressures
- Accelerations
- Temperatures
- Contact between components
Loads can be imported from thermal, flow, and motion Simulation studies to perform multiphysics analysis.
Mesh definition
SOLIDWORKS Simulation offers the capability to mesh the CAD geometry
in tetrahedral (1st and 2nd order), triangular (1st and 2nd order),
beam, and truss elements. The mesh can consist of one type of elements
or multiple for mixed mesh. Solid elements are naturally suitable for
bulky models. Shell elements are naturally suitable for modeling thin
parts (such as sheet metals), and beams and trusses are suitable for
modeling structural members.
As SOLIDWORKS Simulation is tightly integrated inside SOLIDWORKS 3D CAD, the topology of the geometry is used for mesh type:
- Shell mesh is automatically generated for sheet metal model and surface bodies
- Beam elements are automatically defined for structural members
So their properties are seamlessly leveraged for FEA.
To improve the accuracy of results in a given region, the user can
define Local Mesh control for vertices, points, edges, faces, and
components.
SOLIDWORKS Simulation uses two important checks to measure the quality of elements in a mesh:
- Aspect Ratio Check
- Jacobian Points
In case of mesh generation failure, SOLIDWORKS Simulation guides the
users with a failure diagnostics tool to locate and resolve meshing
problems. The Mesh Failure Diagnostic tool renders failed parts in
shaded display mode in the graphics area.